Use case
Milling
Intelligent process monitoring makes it possible to ensure high precision and surface finish requirements on milled parts.
FabOS components used:
Project partners involved
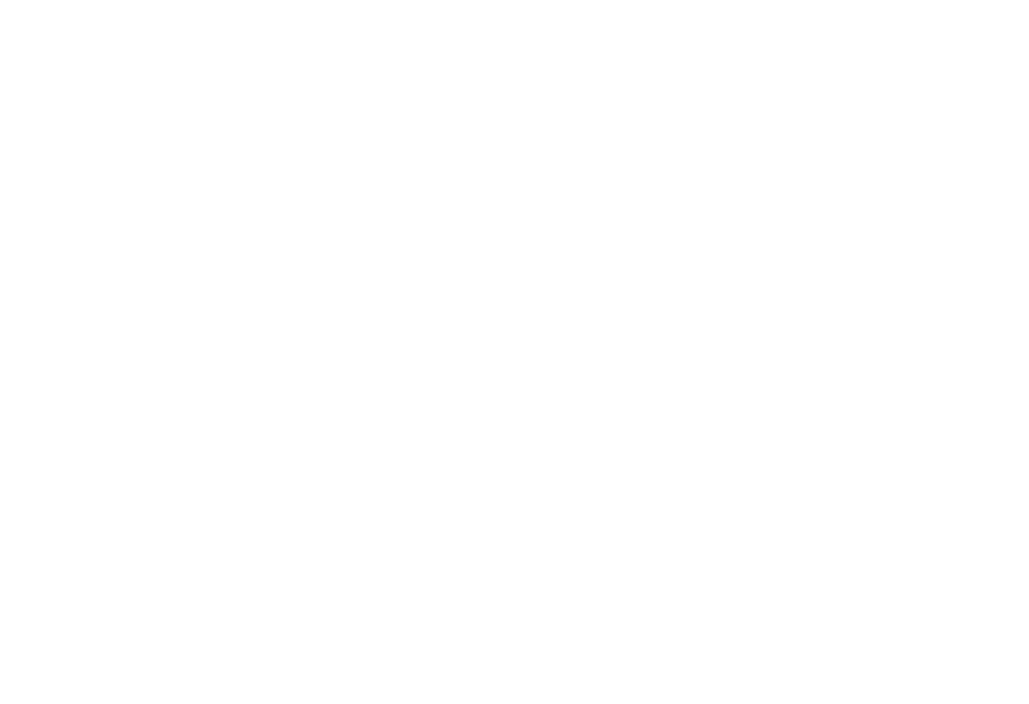
Online process monitoring for highest quality of milled parts
FabOS enables rapid deployment of AI algorithms to monitor the milling process. This makes it possible to detect if and when tool wear and other anomalies, such as the regenerative effect, occur during production.
Project partners involved
Problem:
- Milled parts are often subject to the highest demands for precision and surface finish.
- During manufacturing, anomalies, such as the regenerative effect, may occasionally occur, resulting in defects in the surface finish of the part.
- To guarantee the quality of the workpiece, it often needs to be replaced preventively before the end of its actual service life.
- A complete inspection of all components is time-consuming and costly.
Solution approach:
- Monitoring of the milling process with multiple sensors that are sampled at high sampling rates and synchronized in time.
- AI-based processing of the sensor data enables the detection of tool wear and anomalies during production. The exact moment of occurrence of problems is recorded and transmitted.
- This means that only the relevant components can be subsequently checked at specific points.
Components
Added value through FabOS
- FabOS consistently uses management shells to describe hardware and software. These enable the integration and exchange of additional sensors and evaluation algorithms for further functionalities.
- FabOS simplifies the deployment and lifecycle management of all components.
- FabOS thus enables the simple use of process monitoring in your production as well.
Your contact for questions
Andre Gilerson
Fraunhofer IPT
https://usebasin.com/f/7b119346f966