Use case
Bin Picking
Gripping parts from crates is a common problem in many factories and presents significant challenges.
FabOS components used:
Project partners involved
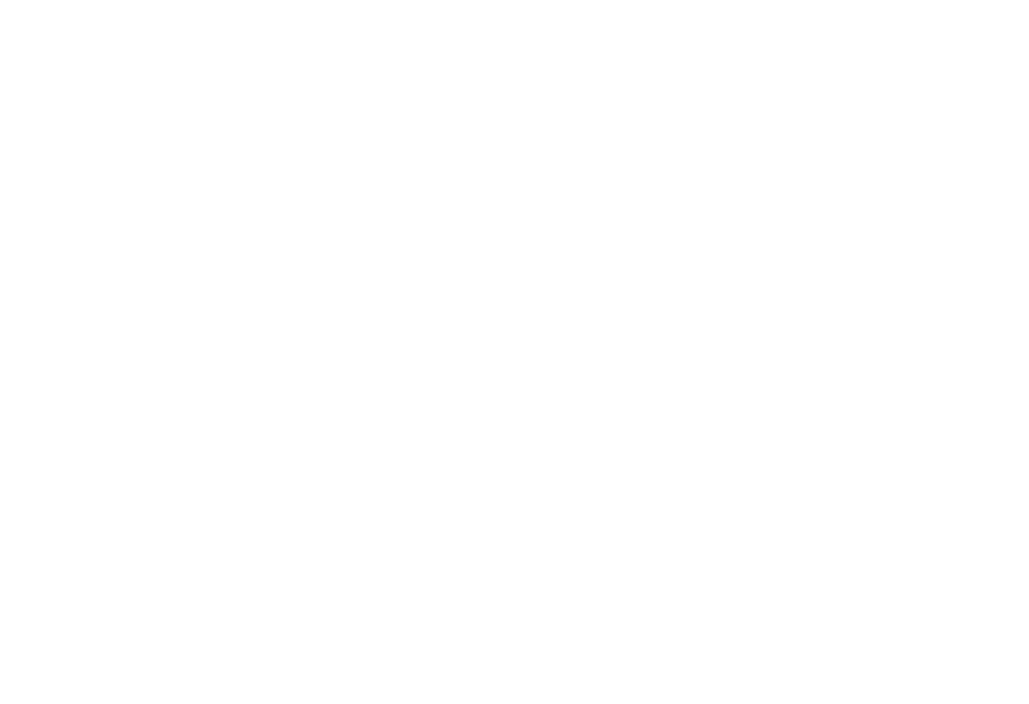
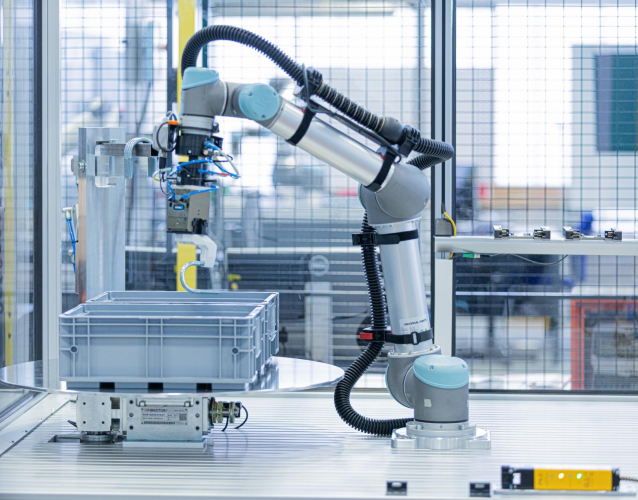
Robust and fast automated separation of parts
With the help of AI methods, all kinds of chaotically stored parts can be picked out of bins. Die automatic training pipeline enables simple teaching of new workpieces without the need for expert knowledge. Additionally, FabOS allows a fast deployment to several robot cells.
Project partners involved
Problem:
- Parts have to be separated automatically from crates that are filled chaotically and sorted by type.
- The separation must be performant enough to maintain the line's cycle.
- The part type in the boxes is unknown and must be identified automatically.
- Depending on the production environment, different hardware is used (e.g. different robots or cameras), requiring a high level of manual adaptation for commissioning.
Solution approach:
- Recording of the situation in the box by 2D & 3D cameras.
- AI-based processing of 2D camera images for part recognition without additional training for new part types.
- Determination of the best grip strategy using AI through 3D camera images.
- Easy teach-in of new parts through automatic training pipeline.
Components
Added value through FabOS
- FabOS consistently uses the digital twin to describe hardware and software to enable the integration and interchangeability of robots and cameras from different manufacturers.
- FabOS makes it possible to use the handle-in-the-box solution in your production as well.
- FabOS provides the software services needed to reach into the box with one click.
No items found.
Your contact for questions
Dr.-Ing. Felix Spenrath
Fraunhofer IPA
https://usebasin.com/f/ce51ffcc6e7f