Use case
Measuring
AI based solutions do support the processes in a versatile production beginning at the material provision with smart carrier boxes, over the set-up of intelligent workpiece carriers, the active temperature control of workpieces up to the temperature supervised measurement process.
FabOS components used:
Project partners involved
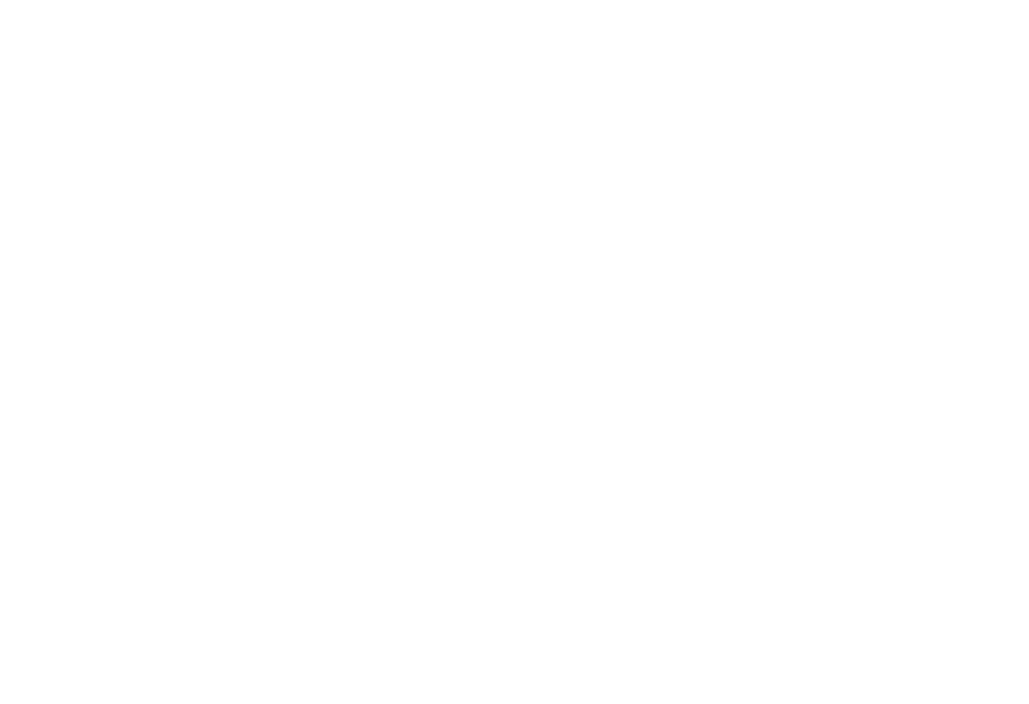
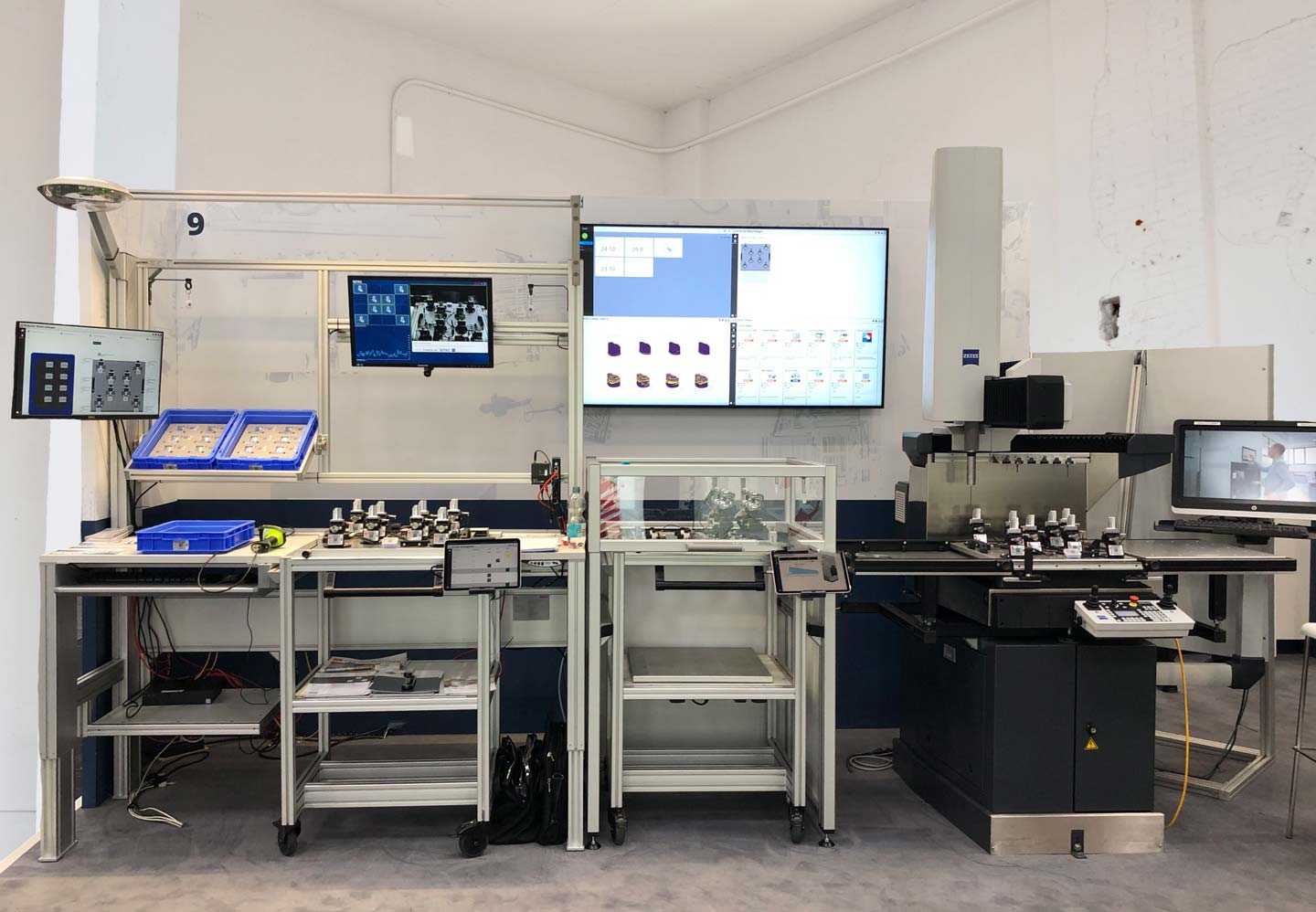
AI supported WebApps do reduce errors, facilitate the operation of machines, and accelerate the quality assurance
The FabOS operating system for the production enables fast deployment of WebApps, backend services, asset administration shells, newly trained AI algorithms using open, harmonized methods onto various aiming systems also without internet connection. With this offer the way to provide and exchange software and information within the production becomes much easier. As aiming platforms ARM and x86/AMD64 controller used in workplaces, machines, data gateways and edge server, as well as in on-edge or on-premises cloud solutions are supported.
Project partners involved
Problem:
- Missing markings on milled parts make traceability in quality assurance to the manufacturing process difficult.
- The options for loading workpiece carriers are usually ambiguous and provoke errors due to lack of concentration.
- Type, position, orientation and placement accuracy of objects on the workpiece carriers are not available as digital information for subsequent processes.
- Process changes and parameter entries at workstations / machines are made in a less user-friendly manner by keyboard entry.
- Quality assurance in production with random samples is inaccurate or leads to high costs due to 100% inspection.
- The lack of secure data connections to production complicates remote service deployment.
Solution approach:
- In carrier boxes re-writable electronic labels are assigned to the milled parts as unique identification mark.
- A web application “digital worker guidance” leads the employee through the process steps.
- AI supported web applications determine type, position, orientation and placing accuracy of objects and pass information over to secondary processes per MQTT.
- An AI based web application provides a user-friendly voice entry at the temperature control process step.
- Sensor data out of the fabrication process offer pre-measurement information about the workpiece quality and allows cost reduction in the metrology process.
- A trusted nonVPN data connection ensures a bi-directional data exchange of augmented camera data für remote service application.
Components
Added value through FabOS
- Marketplace, AppStore with licensing and WebApp transfer technology to EDGE devices.
- Secured commissioning of hardware and software in the production environment.
- Easy installation of the software with one "click" even without internet connection.
- Documented interfaces and semantics.
- Access to digital twins and twin data through an asset administration shell (AAS) infrastructure.
- Rapid implementation of web applications for various production environments.
- Multiple modular and distributed backend services, useable on different systems on-edge, on-premises or on-cloud
Your contact for questions
Dr. Arnd Menschig
Carl Zeiss Industrielle Messtechnik GmbH
https://usebasin.com/f/cdf4c41e82b0